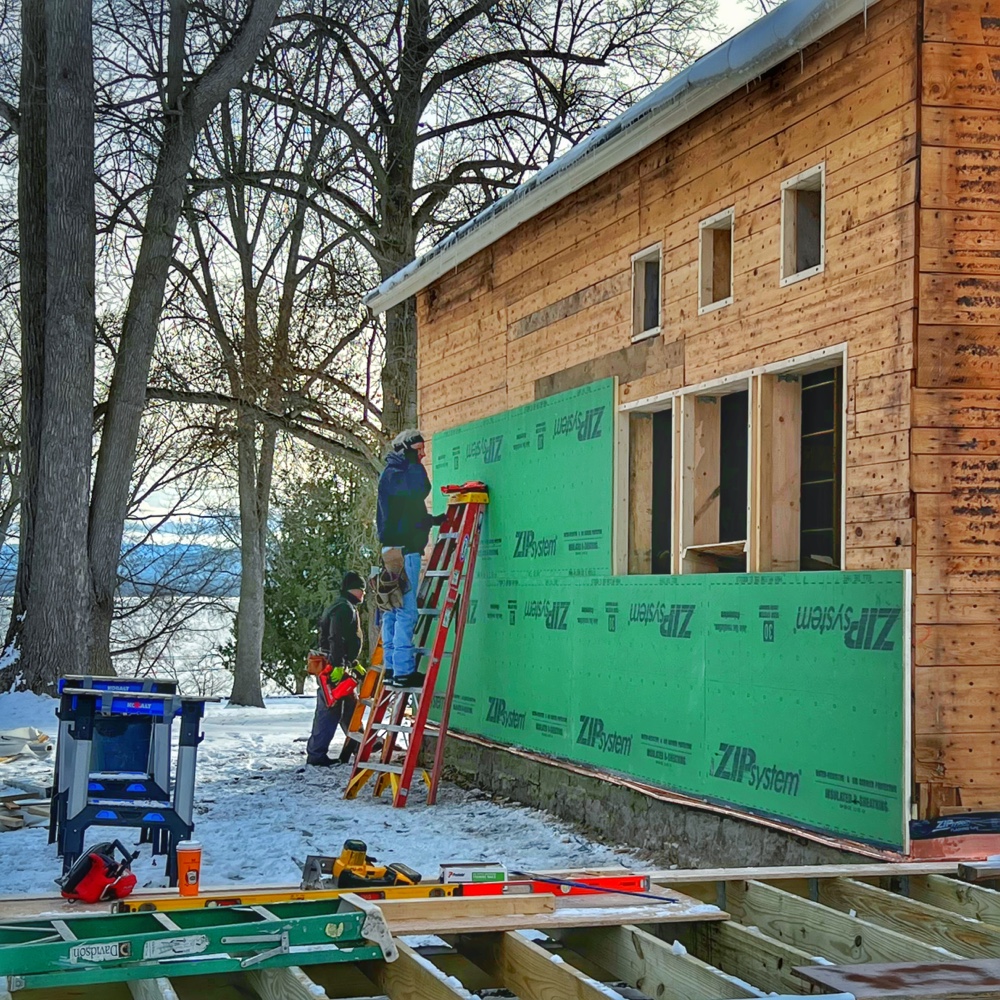
Nothing like a region-wide winter weather system barreling down on you to accelerate winter-proofing the construction site, right?!?! But racing the arrival of a pre-Christmas blizzard isn’t the only motivation for the sudden transformation from 100+ year old T&G sheathing to green ZIP System insulated panels though. We’ve been working toward this goal for weeks. Zipping up the icehouse is actually accomplishing several objectives at once.
Okay, let’s start with the most obvious, short term, practical objective of installing the insulated panels on the exterior of the building. But first, I should qualify what I meant by transforming “100+ year old T&G sheathing to green ZIP System insulated panels.” In this case, transformation does not imply replacing the existing sheathing with the SIPs. Instead, these insulated panels are being installed over top of the existing sheathing. And, as explained previously, the existing sheathing for the icehouse exterior walls is actually two layers of 3/4” T&G sheathing separated by perpendicular furring strips that accommodate ooolllddd school insulation that appears to have been made from shredded newsprint.
Given midwinter construction, adding the ZIP panels efficiently creates a building envelope around the entire structure, allowing interior climate control. Windows and doors will not be delivered and installed until springtime, so this cocoon will stabilize the temperature and humidity for construction while significantly improving the work environment.

That’s the short term, practical objective.
There are some structural benefits as well, augmenting the existing structure (which predates our modern building codes) by creating a structural exoskeleton, that, among other things, dramatically improves sheer strength.
We’re using ZIP System 1-1/2“ thick R-6 insulated panels from Huber Engineered Wood. In addition to insulation and structural objectives, these panels also provide a moisture and air barrier between interior and exterior environments.
ZIP System Insulated R-sheathing is the simple all-in-one structural panel with built-in exterior insulation. Featuring integrated moisture, air and thermal protection, ZIP System R-sheathing completely reimagines traditional wall assemblies by streamlining exterior water, air and thermal management.
Huber Engineered Wood
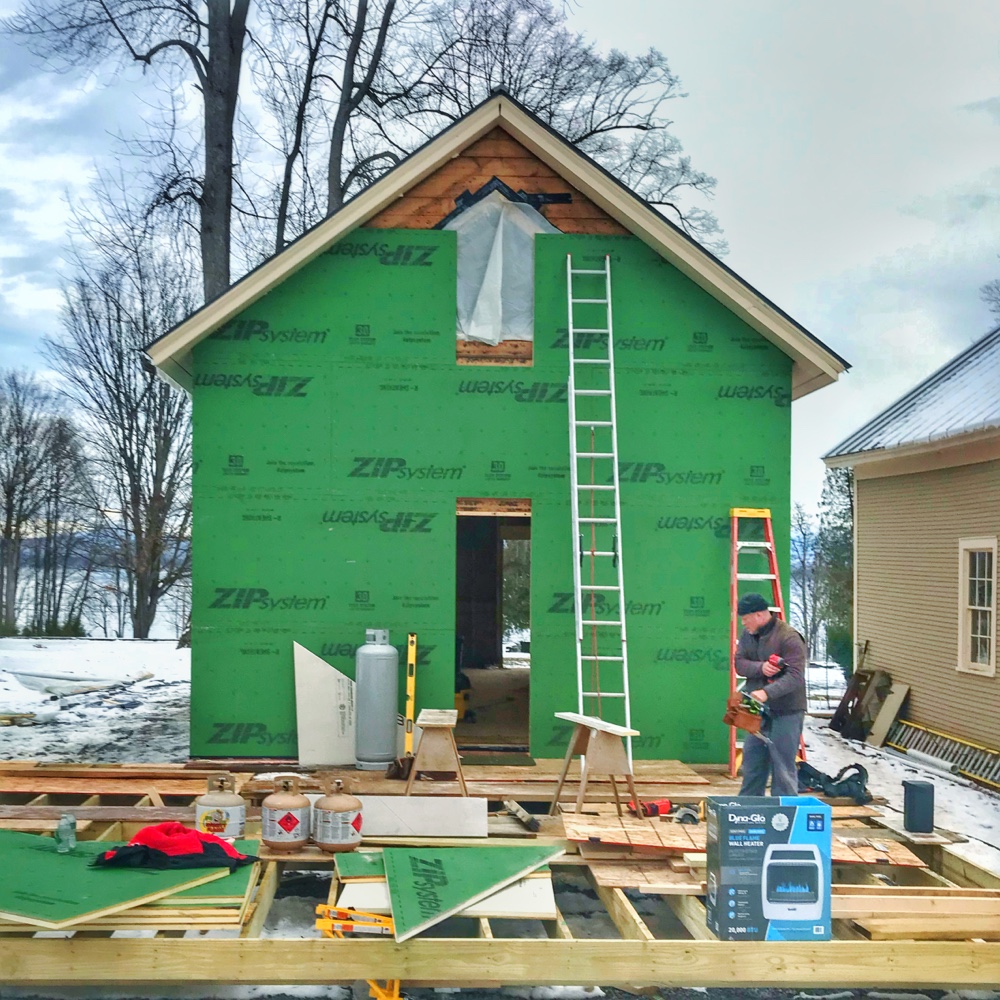
And there are some aesthetic benefits specific yo the icehouse. Preserving the original mortared stone foundation created meant working around inconsistencies such as spots where the framing was proud of the foundation and others where the foundation actually extended out beyond the framing. Aside from the visual incongruities, this has created moisture penetration and rot issues over the building’s many years of service. When we stabilized the structure in 2006-7 it was necessary to replace large sections of the rotten sill. Additional rehabilitation was necessary this fall as well. By adding an extra 1-1/2” skin around the exterior of the icehouse (and integrating a copper drip edge / flashing that isolates wood from masonry) the entire build now overhangs the foundation enough to manage moisture, snow, etc. for another 100+ years.
But wait… There’s more!
The panels are permitting us to tune up some of the geometry — wall planes and trim lines that have deviated and deflected, sagged and bowed over the years — so that the rehabbed icehouse stands proud next summer.
What do you think?