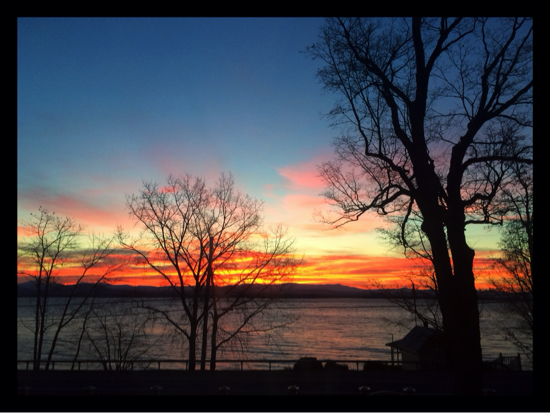
It’s impossible to frown your way into the day with this magnificent view smiling back at you. Even the dreamy distortions of wavy glass don’t spoil the effect. In fact, like so many other old home enthusiasts, I love the wavy the glass!
Homes built before the turn of the 20th century have a very distinct characterization that many homeowners may not completely understand: a wavy appearance that can distort the images behind it… There is a certain charm about wavy glass that gives your home an antique, historical value that many homeowners find appealing. Many… appreciate the authenticity and originality of the wavy windows as contributing elements to the overall style of the home. (Angies List)
Rosslyn has greeted spectacular sunrises for almost two centuries, so the least we can offer as her current custodians is respect for her antique quirks. But preserving (and occasionally replacing) Rosslyn’s wavy glass goes beyond respect for history.
One of the things I absolutely love about old houses and antiques is the minor but striking detail and character that wavy glass brings. It’s one of those little things that screams “I came from a simpler time, where things were still hand made, imperfect, and unique!” (Old Town Home)
What is Wavy Glass?
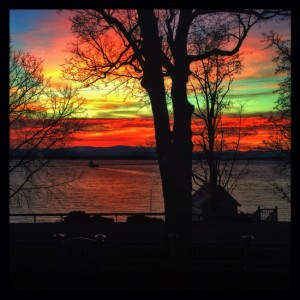
So what exactly is the story with the wavy glass you see in old houses?
Apparently one of the best explanations comes from an article that appeared some time ago in Old House Journal. Although I haven’t successfully laid my hands on the original article yet, the following explanation is ostensibly quoted from the original. It offers as good an explanation as any I’ve seen, and breaks out the two different varieties of wavy glass.
Crown Glass
For centuries, the best quality window glass was crown glass. To make panes with this method, a glass blower gathered a clump of molten glass on the end of a hollow pipe and blew it into a bubble much like a bottle. As a helper attached a pontil rod to the other side of the bubble, the glassworker broke off the blowpipe creating a hole. Then, by heating the glass and coaxing it with a wood paddle, he quickly enlarged this hole into a rough plate.
Working in front of a furnace to keep the glass hot and fluid, the worker then spun he rod with his hands, often on a supporting bench, so that centrifugal force stretched the glass out into a thin disc – a process nearly identical to a baker spinning fresh pizza dough for a pie. When the blower severed the rod, he had a disc of thin glass, up to 4 feet in diameter.
After annealing this table in another oven to equalize stresses, the glass was carefully cut into panes according to grade and size. The central “bull’s-eye” – the thickest and most malformed part where the rods touched – was usually unsalable and returned to the furnace… (Fairview Glass)
Creating crown glass must have been incredibly time consuming and labor intensive. Suddenly the luxury of early glass panes comes into focus. So nostalgia (and that dreamy filter which subtly distorts the view) and historic authenticity are trumped by a third important reason to value and preserve wavy glass. It retains the intimate contact and hard work of a human being. As old home owners we should feel obligated to honor that enduring investment of human labor.
Cylinder Glass
Learning about crown wavy glass offers an almost romantic glimpse into window’s patina’ed to past. And yet the inefficiency is obvious, and innovation was inevitable.
Though crown glass was made up to the 1850s, it could not supply the need for bigger panes created by a growing population. The glass that could was cylinder glass (also called broad glass or sheet glass), and it dominated this industry for the rest of the century.
To make cylinder glass, the glassworker blew a large tube of glass. After cracking off the blowpipe, the glassworker cut off the ends and slit the tube down one side. From here these shawls were transferred to a special oven where they could wilt and unfold into a flat sheet.
By the 1870s, glass manufacturers were adding pits dug deep in the floor of the glass factory to allow blowers to swing the glass as they blew. The resulting cylinders were up to 18 inches in diameter and a remarkable 7 feet in length.
Two decades later, some manufacturers had mechanized the steps with cranes and compressed air. These cylinders made possible by the Lubbers process – the last before the switch to drawn-sheet glass manufacturing in this century – were several feet in diameter. (Fairview Glass)
Cranes and compressed air?!?! My commitment has been renewed to preserve and enjoy the nuances of Rosslyn’s wavy glass… And you? What’s your take on wavy glass?
What do you think?